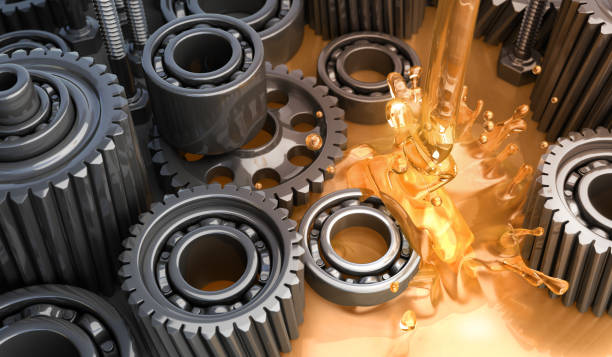
How to Identify and Address Common Lubrication Issues
Proper lubrication is essential for keeping machinery and equipment running smoothly and efficiently. However, even with the best maintenance practices, lubrication issues can arise, leading to increased friction, wear, and potential equipment failure. In this blog post, we’ll discuss some common lubrication issues, how to identify them, and steps to address them effectively.
1. Over-Lubrication and Under-Lubrication
Issue: Over-lubrication occurs when too much lubricant is applied, leading to excess grease or oil buildup, increased friction, and potential leaks. Under-lubrication, on the other hand, results from insufficient lubricant application, leading to increased wear and friction between moving parts.
Identification: Signs of over-lubrication include excessive grease/oil leakage, overheating, and increased energy consumption. Under-lubrication may manifest as abnormal noise, increased vibration, and premature wear on machinery components.
Addressing the Issue:
- Follow manufacturer recommendations for lubrication quantities and intervals.
- Implement regular inspections to ensure proper lubricant levels and adjust as necessary.
- Use automated lubrication systems to control and monitor lubricant application accurately.
2. Contamination
Issue: Contamination occurs when foreign particles such as dust, dirt, water, or metal shavings enter the lubrication system, leading to abrasive wear and reduced lubricant effectiveness.
Identification: Signs of contamination include visible dirt or debris in lubricant samples, abnormal wear patterns on machinery components, and increased friction and temperature.
Addressing the Issue:
- Store lubricants in clean, sealed containers to prevent contamination.
- Implement proper filtration systems to remove contaminants from lubricants.
- Regularly inspect and clean lubrication system components, such as filters and reservoirs.
3. Mixing Incompatible Lubricants
Issue: Mixing incompatible lubricants can lead to chemical reactions, reduced lubricant effectiveness, and equipment damage. Different lubricants have varying viscosities, additive packages, and base oils, making them incompatible with each other.
Identification: Signs of incompatible lubricant mixing include changes in lubricant color, consistency, or performance, as well as equipment malfunction or failure.
Addressing the Issue:
- Clearly label lubricant containers and storage areas to prevent mix-ups.
- Thoroughly flush and clean equipment before switching lubricants.
- Consult with lubricant suppliers or experts to ensure compatibility when using different lubricants.
4. Improper Lubricant Selection
Issue: Using the wrong type of lubricant for specific applications can lead to poor performance, increased wear, and equipment damage.
Identification: Signs of improper lubricant selection include excessive friction, overheating, equipment malfunction, and premature component failure.
Addressing the Issue:
- Consult equipment manuals and manufacturer recommendations for appropriate lubricant selection.
- Consider factors such as operating conditions, temperature, load, and speed when choosing lubricants.
- Test lubricants in controlled conditions before full-scale implementation.
Conclusion
Identifying and addressing common lubrication issues is essential for maintaining equipment reliability, performance, and longevity. By implementing proper lubrication practices, conducting regular inspections, and addressing issues promptly, you can minimize downtime, reduce maintenance costs, and extend the lifespan of your machinery and equipment.
At BES CO LTD, we offer a range of high-quality lubricants and expert advice to help you optimize your lubrication practices and keep your equipment running smoothly. Contact us today to learn more about how we can support your lubrication needs.
Leave a Reply