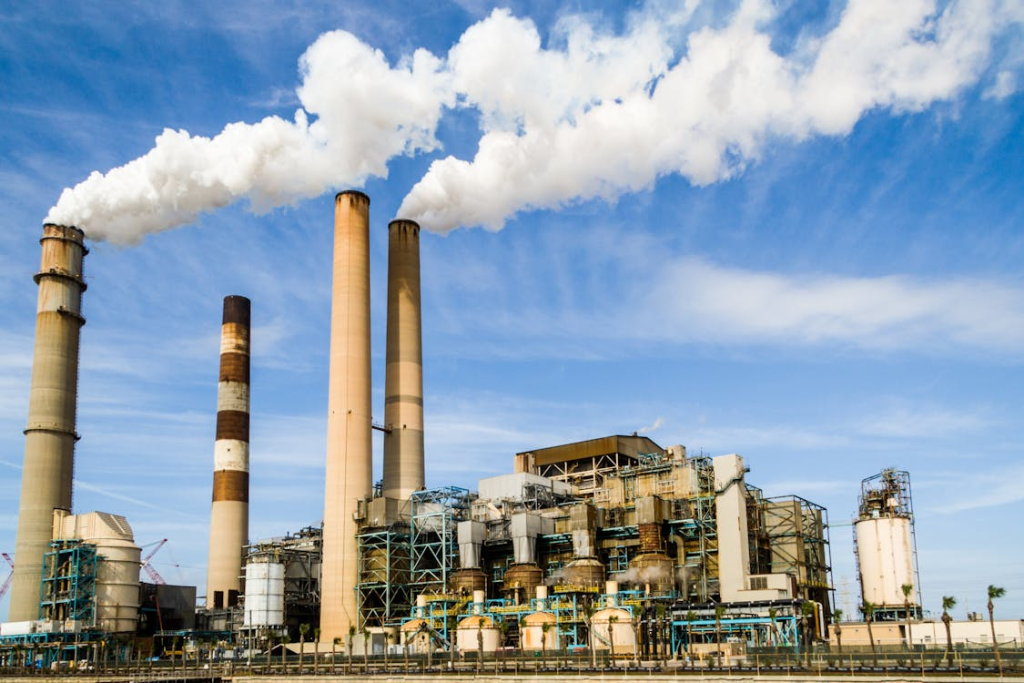
Tips for Optimizing Industrial Equipment Performance
In the fast-paced world of manufacturing and industrial operations, maximizing the performance and efficiency of equipment is essential for maintaining competitiveness and profitability. Whether you’re running a factory, a construction site, or a production facility, optimizing industrial equipment performance can lead to significant cost savings, improved productivity, and reduced downtime. In this blog post, we’ll explore some practical tips to help you get the most out of your industrial equipment.
1. Regular Maintenance and Inspections
One of the most important aspects of optimizing industrial equipment performance is regular maintenance and inspections. Establish a proactive maintenance schedule and conduct regular inspections to identify and address issues before they escalate. This includes:
- Routine Lubrication: Ensure that all moving parts are properly lubricated according to manufacturer recommendations to minimize friction and wear.
- Cleaning and Calibration: Keep equipment clean and calibrated to prevent build-up, corrosion, and inaccuracies that can affect performance.
2. Train and Empower Your Team
Invest in training programs to ensure that your team members are properly trained in the operation and maintenance of industrial equipment. Empower them to identify potential issues and perform basic troubleshooting to address minor problems before they lead to downtime. Well-trained operators are more likely to use equipment efficiently and safely, leading to improved performance and longevity.
3. Monitor Performance Metrics
Implement a system for monitoring key performance metrics of your industrial equipment, such as:
- Downtime: Track downtime events and analyze their causes to identify opportunities for improvement.
- Utilization: Monitor equipment utilization rates to identify underutilized or overutilized assets and optimize scheduling accordingly.
4. Implement Predictive Maintenance
Consider implementing predictive maintenance techniques, such as condition monitoring and predictive analytics, to anticipate and prevent equipment failures. By monitoring equipment performance in real-time and analyzing data, you can identify signs of potential issues and take proactive measures to address them before they impact operations.
5. Optimize Workflows and Processes
Review your workflows and processes to identify opportunities for optimization and efficiency gains. This may include:
- Streamlining Processes: Eliminate bottlenecks and unnecessary steps in production processes to improve efficiency and throughput.
- Optimizing Equipment Layout: Arrange equipment layout to minimize material handling and reduce cycle times.
6. Upgrade to Energy-Efficient Equipment
Consider upgrading to energy-efficient equipment and technologies to reduce energy consumption and operating costs. Energy-efficient equipment not only reduces environmental impact but also lowers utility bills and improves overall operational efficiency.
7. Invest in Quality Spare Parts and Components
Using high-quality spare parts and components is crucial for maintaining the performance and reliability of industrial equipment. Choose OEM parts or reputable aftermarket suppliers to ensure compatibility and reliability. Avoid cheap, low-quality parts that may compromise equipment performance and safety.
Conclusion
Optimizing industrial equipment performance is essential for maximizing productivity, reducing costs, and staying competitive in today’s fast-paced industrial landscape. By implementing these tips, you can improve equipment reliability, extend asset lifespan, and achieve better overall operational efficiency. At [Your Company Name], we’re committed to helping you optimize your industrial equipment performance with our high-quality products
Leave a Reply